Helmet Liner
While working for D3O (impact protection company) i was assigned to lead and design a platform technology that can be adapted and pass various standards for sports helmets. The initial target was american football helmets, at a time were the US congress was considered restrictions or banning tackles, due to numerous cases of players getting concussions and permanent brain damage. The final product had to pass and be certified according to the NOCSAE standard.
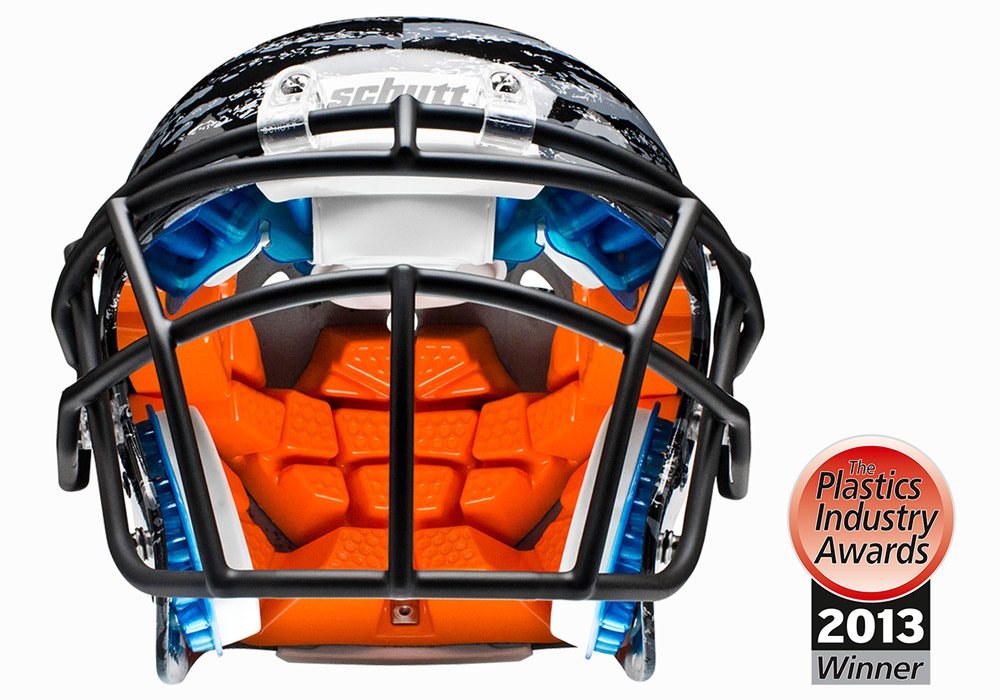
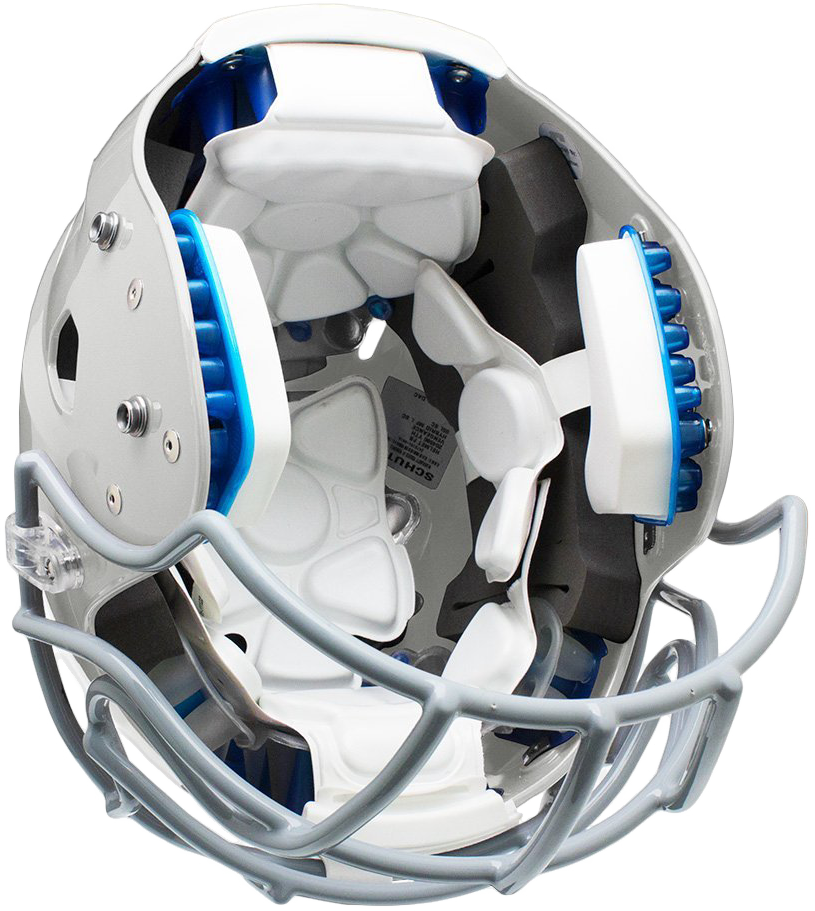
Issues with existing products
- Foam of different thickness and stiffness is used in the same helmet as the human head is not a perfect sphere and impact requirements are different in each area.
- Fabric and open cell foam are hard to clean. Helmets become smelly and unpleasant.
- High tooling cost to produce all the parts.
- Open cell foam incubates MRSA bacteria, some resistant to antibiotics. Several hi profile players contracted those over the resent years.
- Complicated/expensive assembly (manual) and big inventory of parts.
- Time consuming reconditioning (repair).
Design Solution
During this project a new material was created to pass the NOCSAE standard and I also developed a process of coating the liner with TPU film in the tool. The performance had to be similar in any location but as the helmet has irregular shape, I had to optimise the volume of material in each area taking into account fit, breathability, comfort, weight and material properties. The result is aesthetically pleasing and looks simple, but required an immense amount of testing to fine tune.
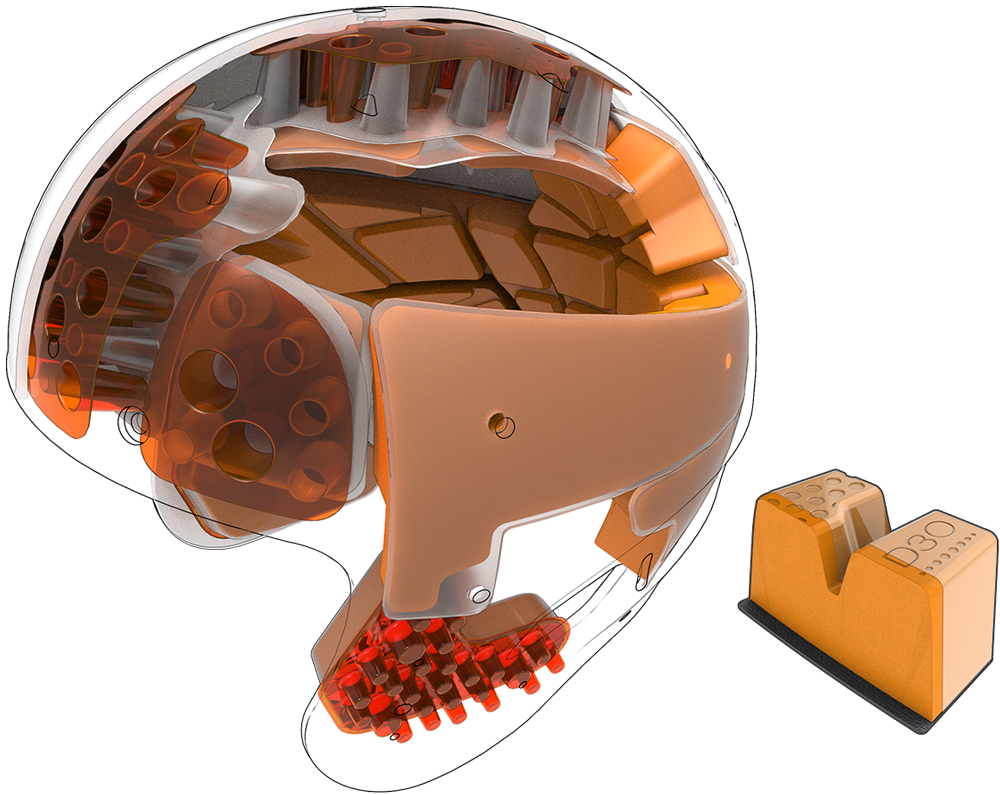
Product Development Process
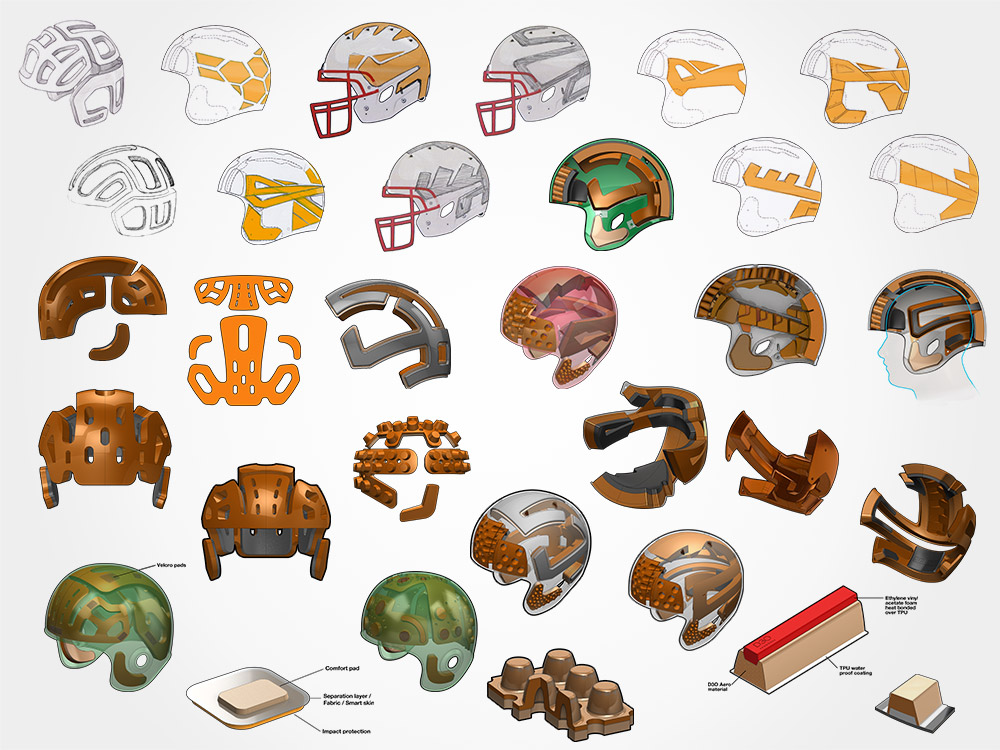
Brainstorming
Initial concepts concentrating on engineering solutions rather than aesthetics, as the company did not have the know how or suitable material for use in helmet applications.
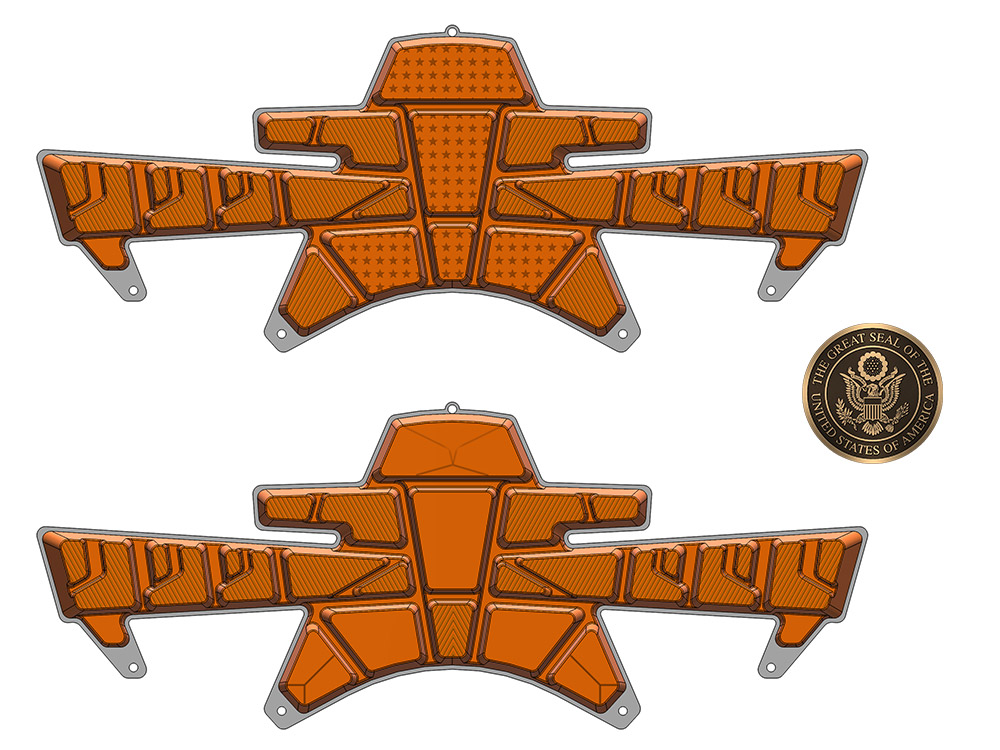
Concept Design
After initial R&D once the engineering requirements were understood, i proceeded to concept design. The aesthetics were based on iconic American symbols and was well received by the client.
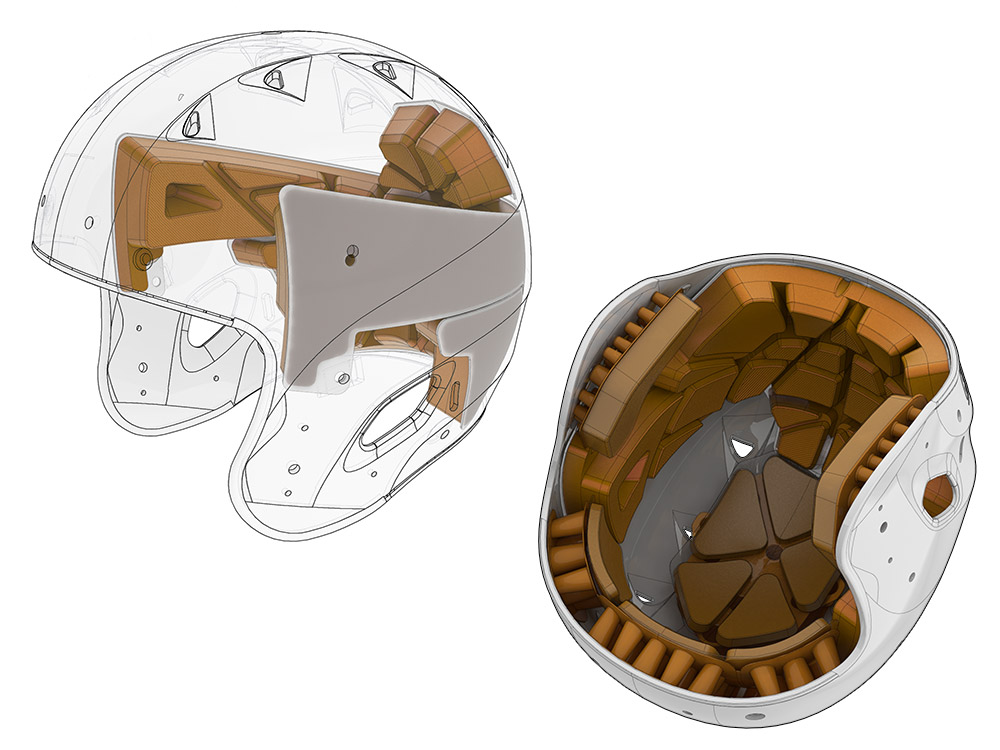
Final Concept & CAD
The part, moulded flat would deform inside the helmet. To preserve the concept’s aesthetics i modeled the part inside the helmet to calculate deformation and the precise dimensions of the flattened geometry.
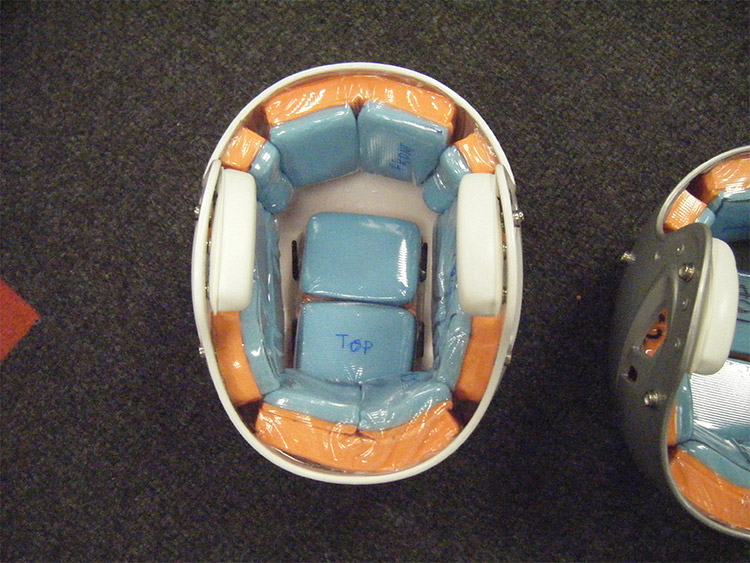
Preliminary testing
Existing D3O material was not suitable for helmet use. These were tested inside helmets to determine a baseline and figure the resources needed to improve it up to the point of passing the relevant standards.
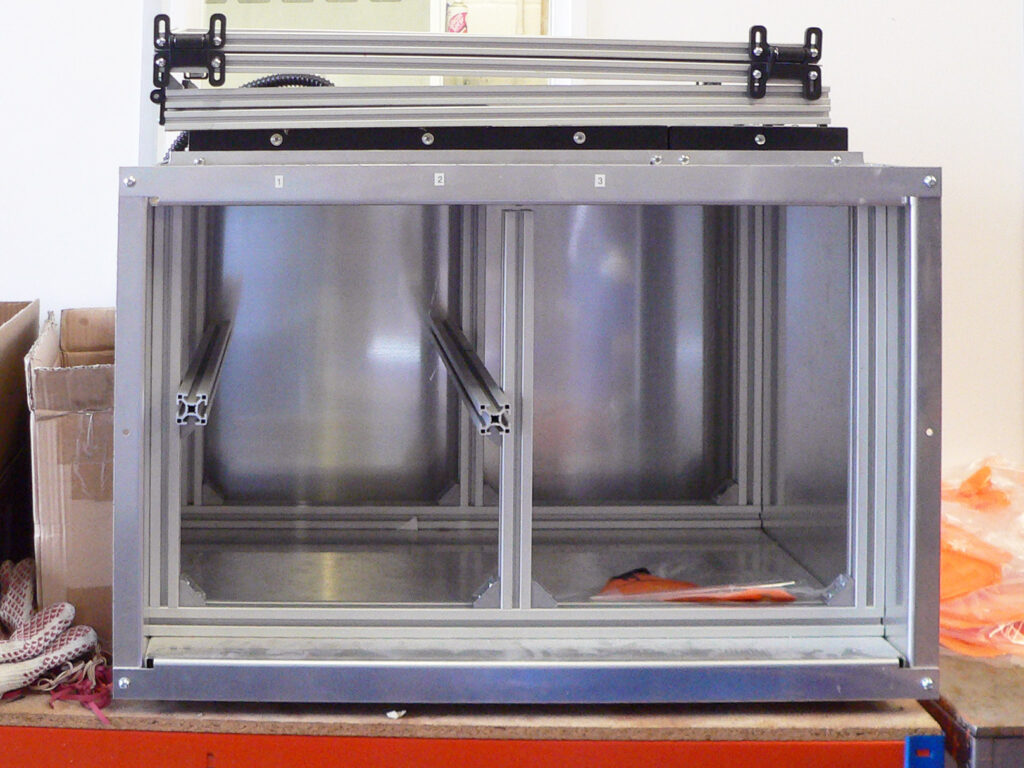
Design equipment
During this project i also sourced equipment needed for manufacturing of the prototypes (and subsequently production) such as a vacuum pump and designed an oven to heat sheets of materials for vacuum forming.
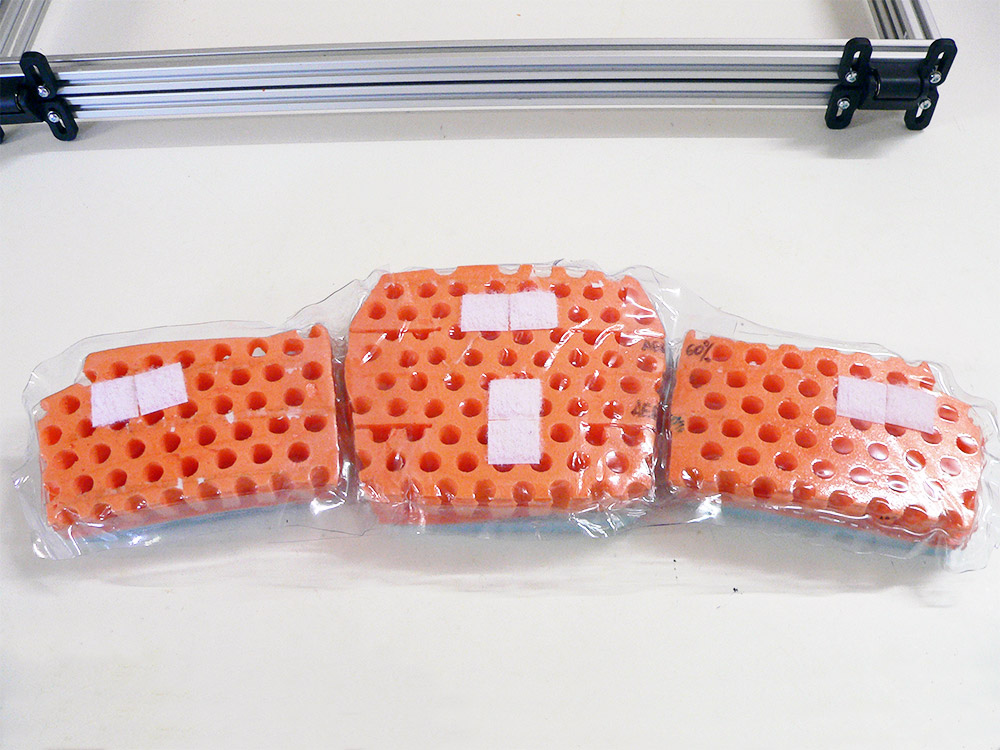
Testing
I produced more than 40 full size prototypes which were impact tested in order to understand the relation between material hardness, thickness and coverage in different areas of the helmet. A much bigger number of small scale samples were produced while developing the final material.
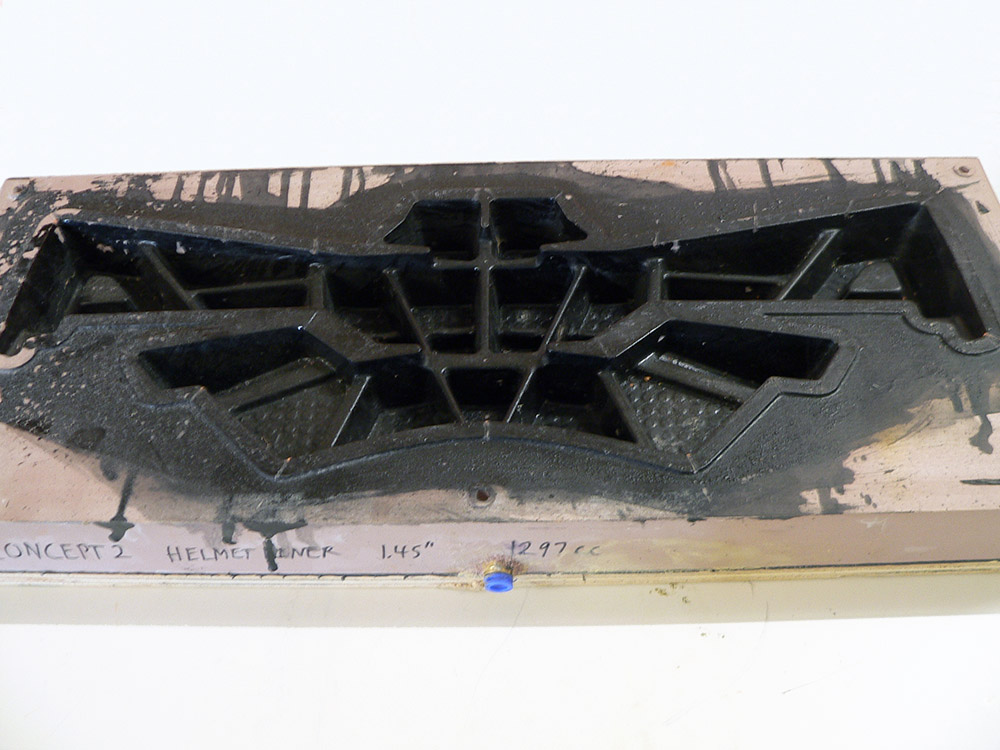
Prototype tooling
Designed a tool for vacuum forming film and overmoulding with polyurethane in the same cavity. This was cut in-house and coated to improve longevity. The underside of the tool has a vacuum chamber and connects to a pump.
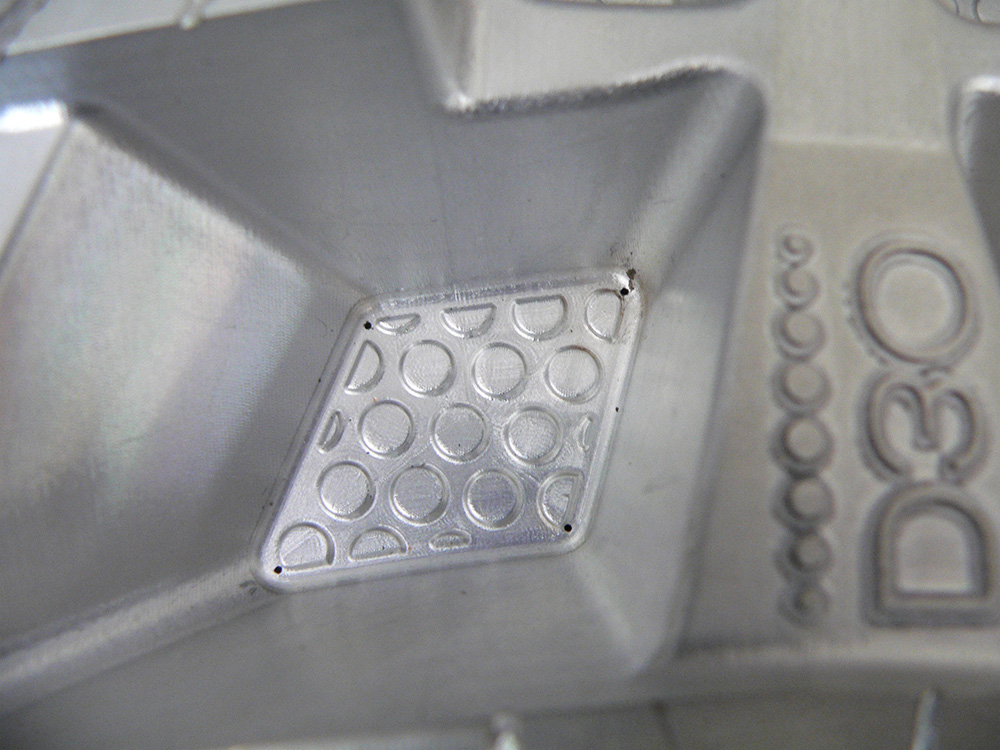
Vacuum forming
I troubleshoot the vacuum forming process, so the surface pattern had good definition, the film was not creasing or bursting. This was done by drilling and plugging pin size holes on the soft tool. Image from the production tool.
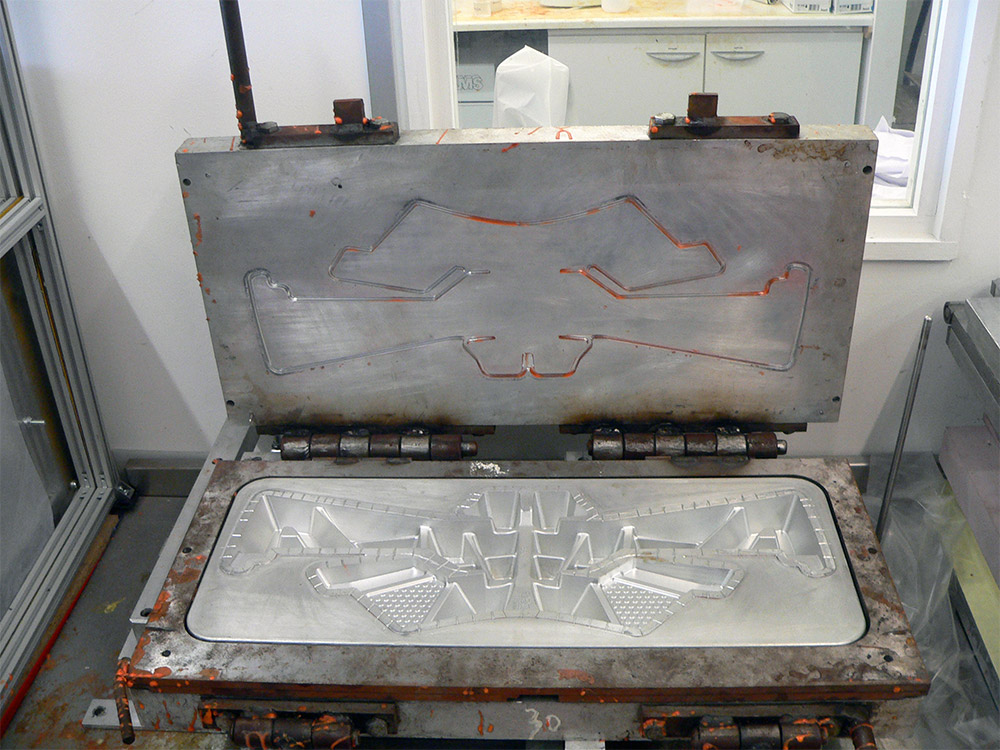
Production tool
Production tool was designed and tested / troubleshoot in UK. Production of parts were subcontracted in China.
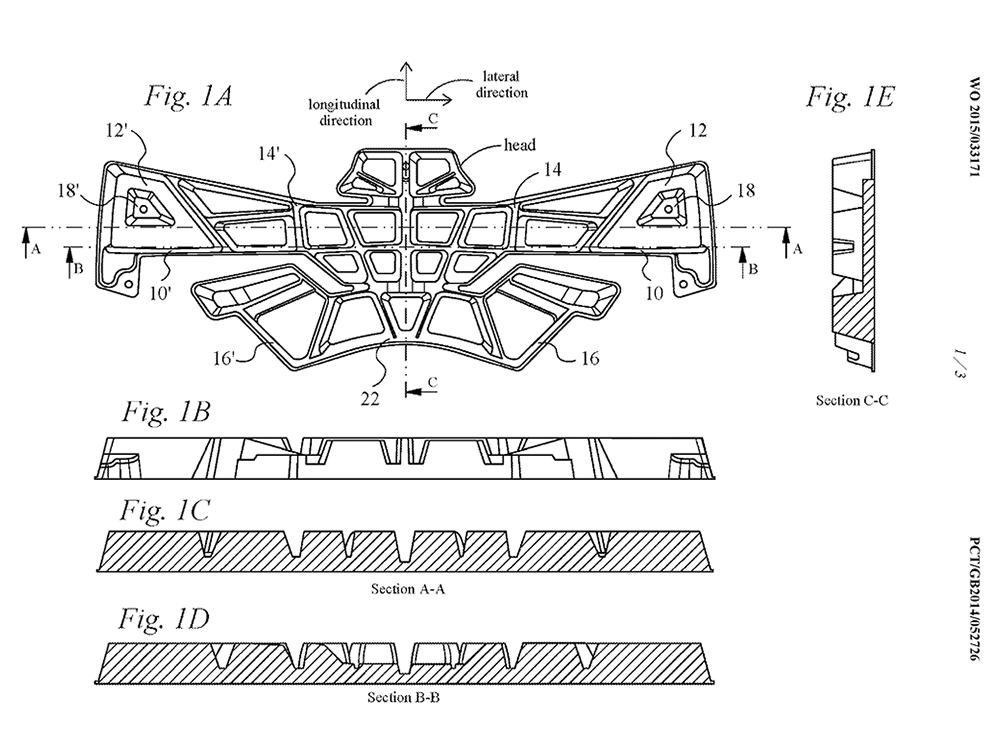
Patent
The product was awarded Product Design of the Year in UK’s popular Plastic Industry Awards and the technology is patent. This opened the helmet market for D3O and attracted more clients.
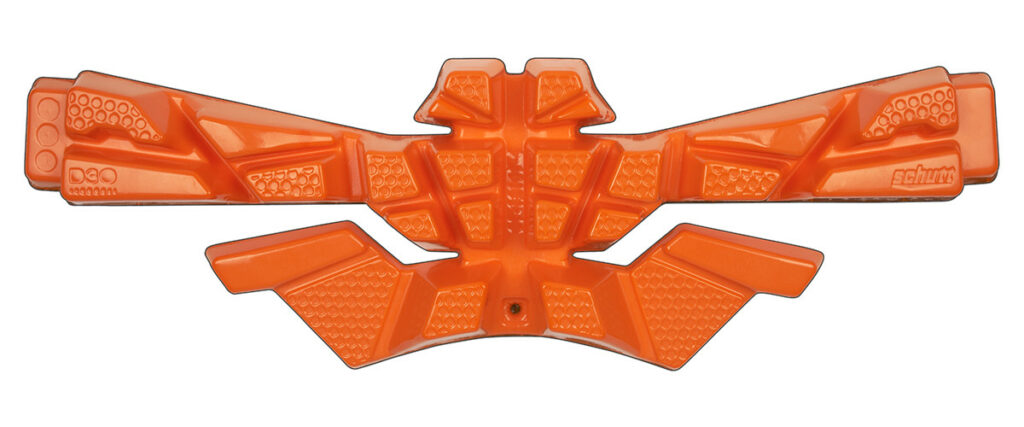
Production parts
The project took 8 months from concept to production, won an initial contract for over ½ million dollars and led D3O to start a separate department and further contacts including military.
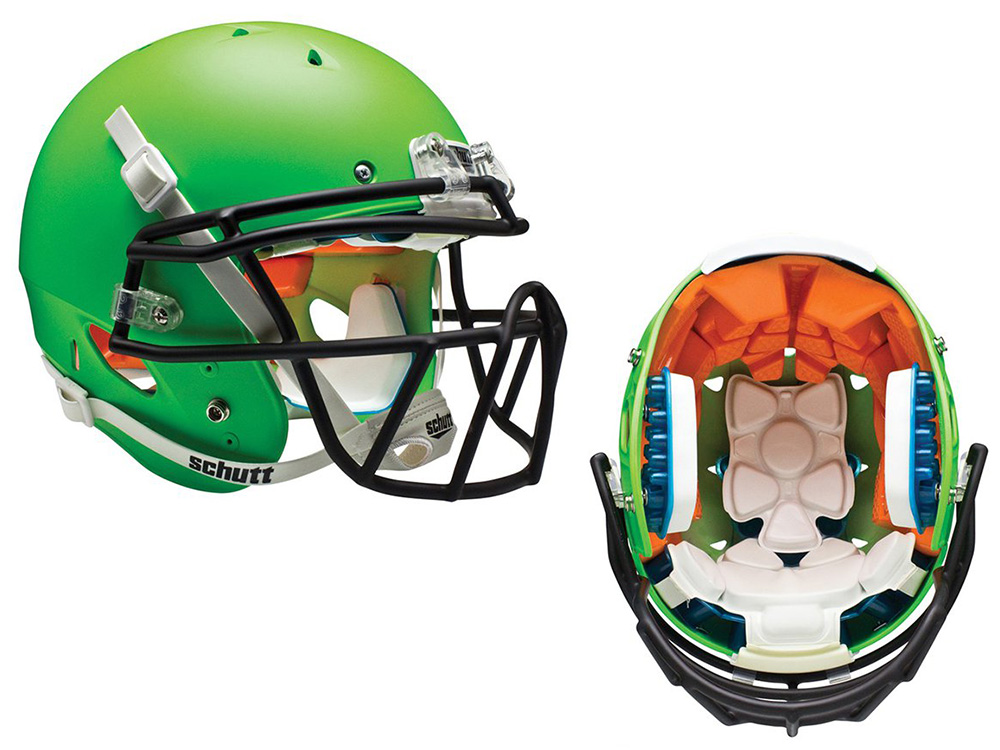
Final product
There are 6 sizes of liner fitted in 3 different helmet models with a few sizes each. This creates a large combination of products that fit comfortably to most users and make the product feel customized.