Industrial PC
Working for Captec I took part in developing an IP66 industrial PC. The product has a back from SPZ (vacuum formed zinc alloy), a process ideal for small volume production without the costs of plastic injection moulding tooling.
I was responsible for part of the concept work, modelling the back, the majority of the metalwork and took active or leading part in the development. Product features:
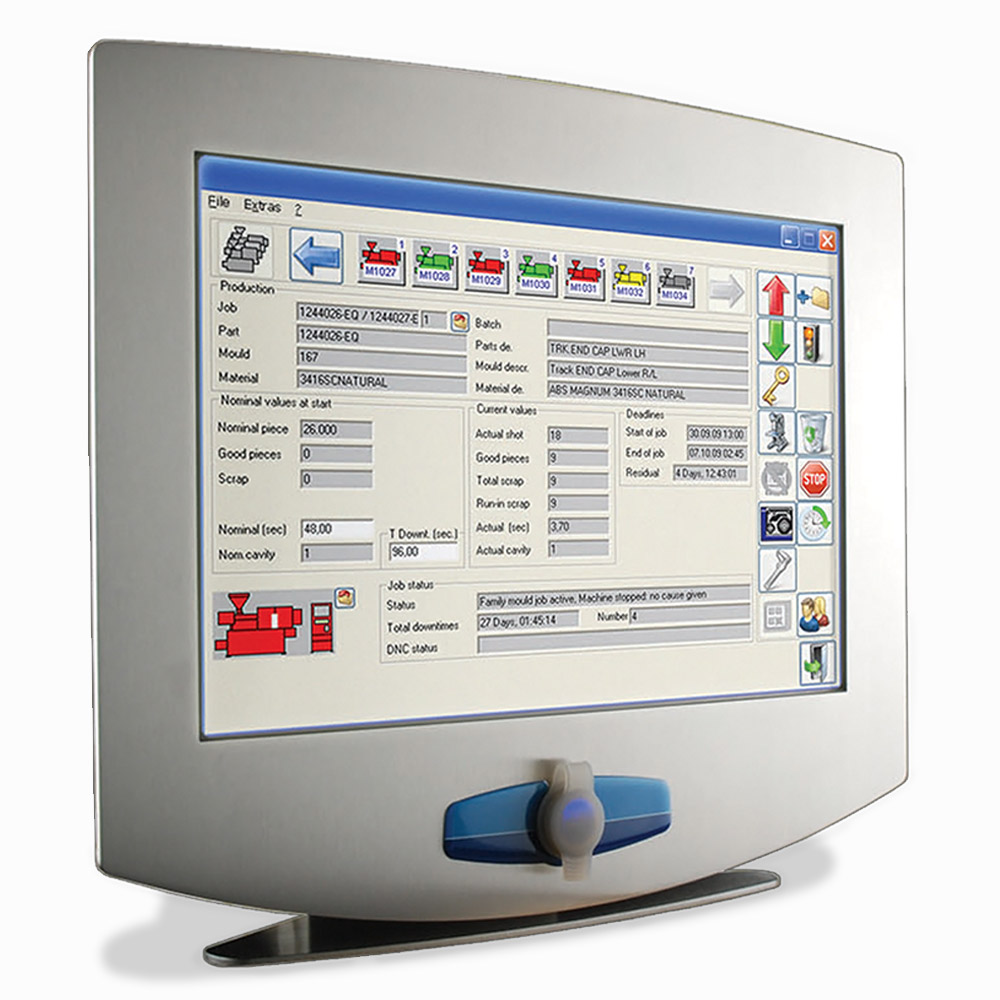
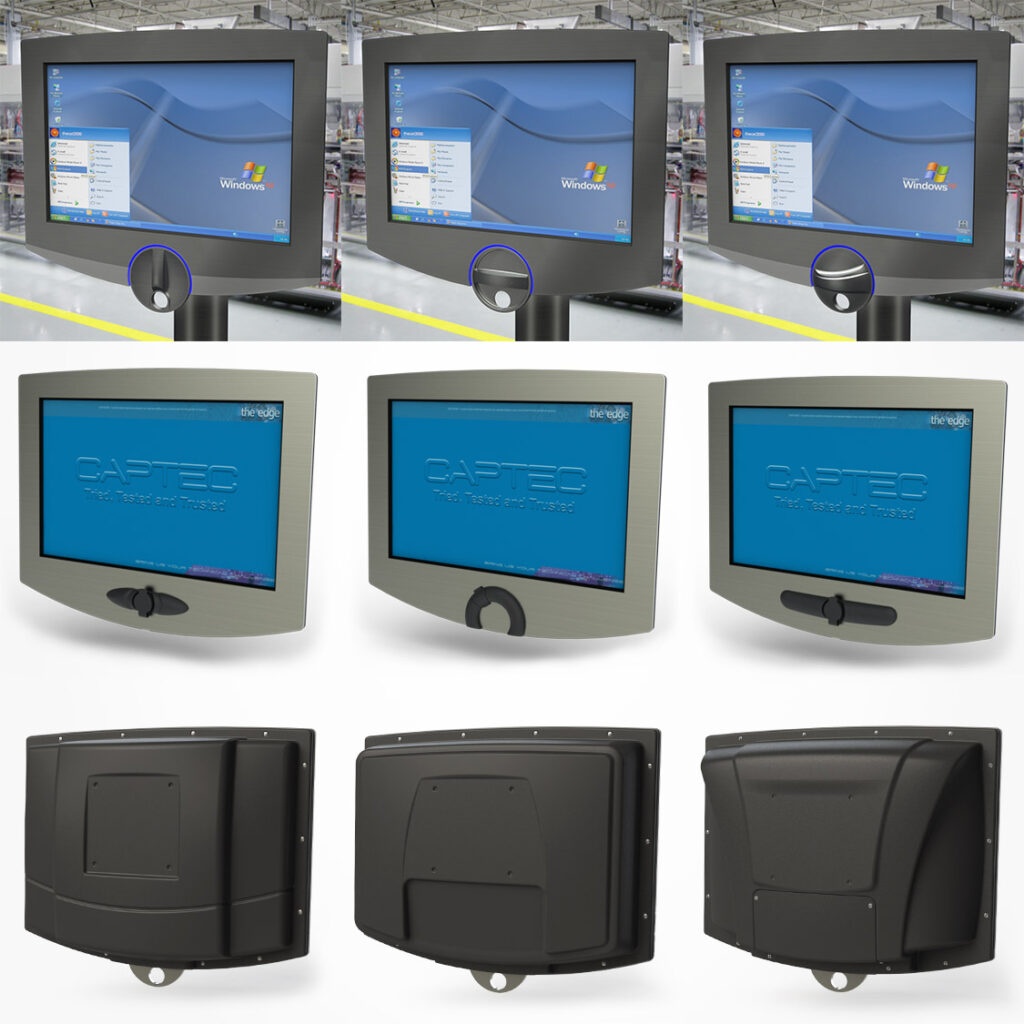
Concept Design
Since the beginning of the project they were 2 predominant ideas for interface. One were the power button and USB port was accessible through a rotating knob. The second was a rubber cover revealing the above inputs. I created a series of concepts for every aspect of the unit and cost them for the management team to make an informed decision. This involved detailing a few concepts for manufacturers to quote.
Simulation and CAD
Back and metalwork create and air duct on the IP44 version. The cold air enters the unit and and travels through components placed on order of importance, HDD, CPU and memory and finally power supply.
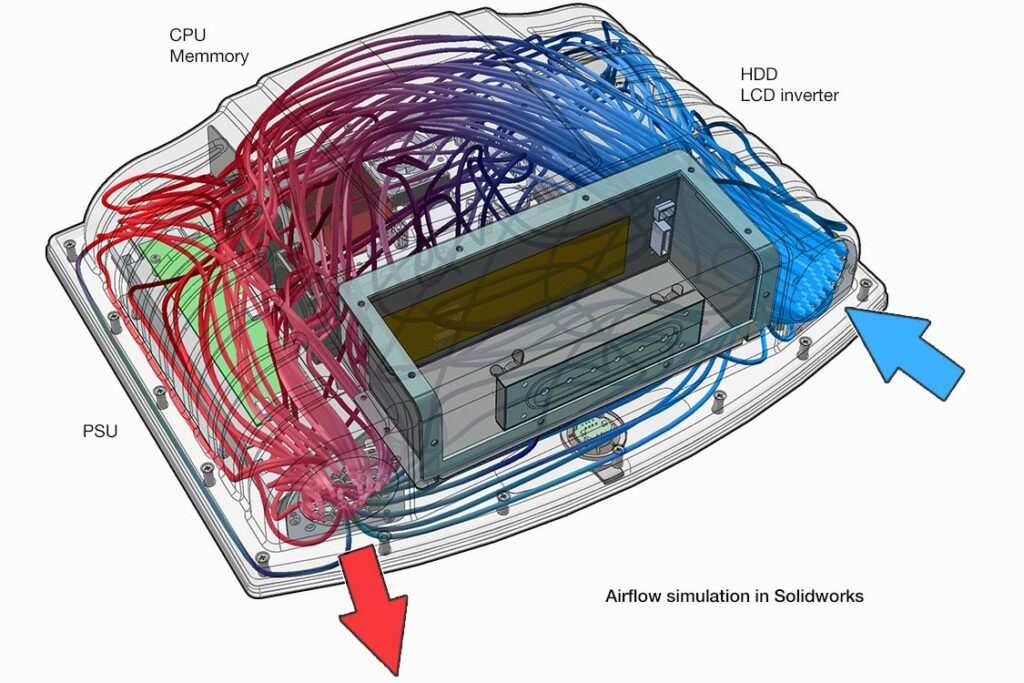
Engineering and Production
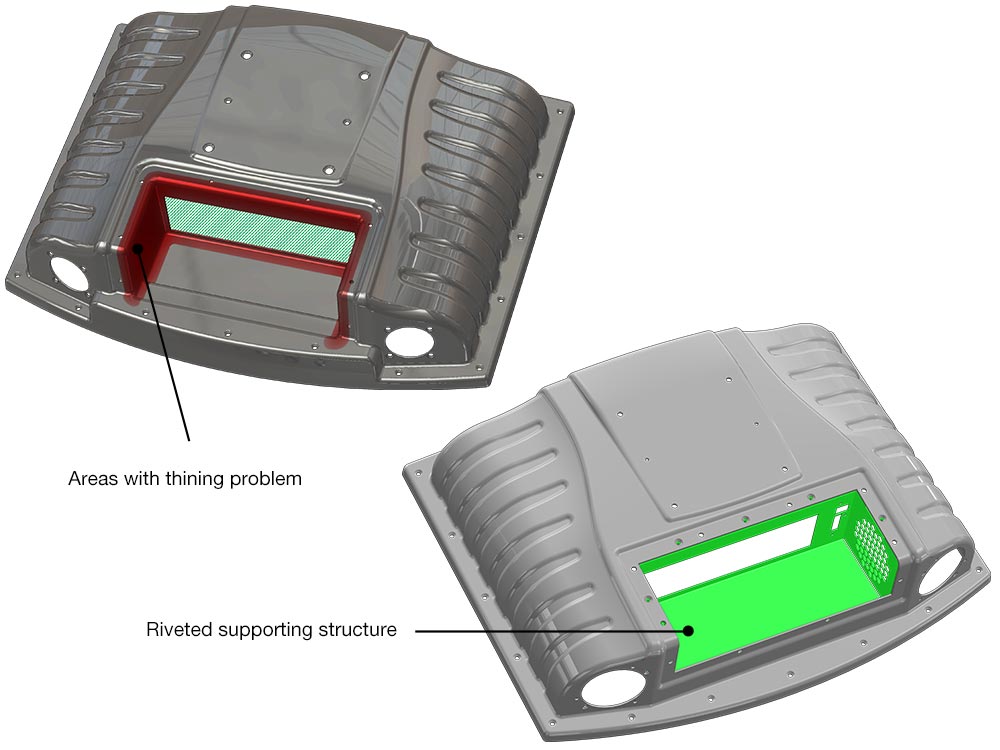
SPZ Back (Super Zink Alloy)
The back of the unit was made from vacuum formed SPZ. As tooling is cheap it was the best option for a mid volume production of such a curved shape. The initial design would end up in material thinning around the cable bay so this are was replaced with a folded sheet.
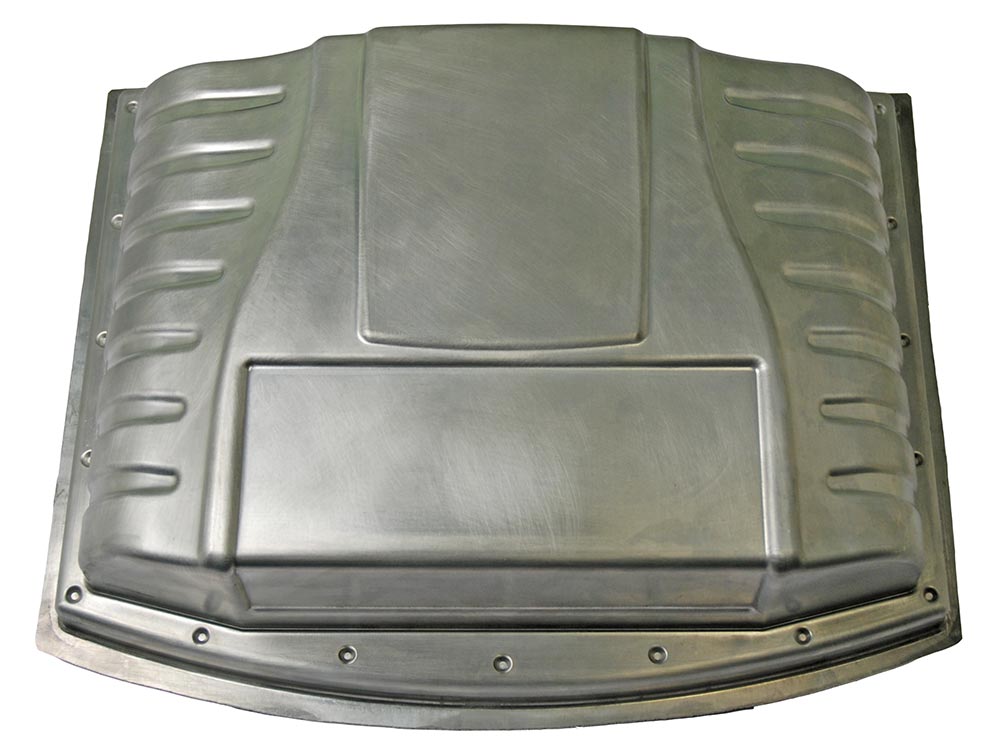
First article approval.
First batch of parts was inspect. I tested the VESA area of the back which could withstand more 1000N (target value) of vertical load without the part distorting.
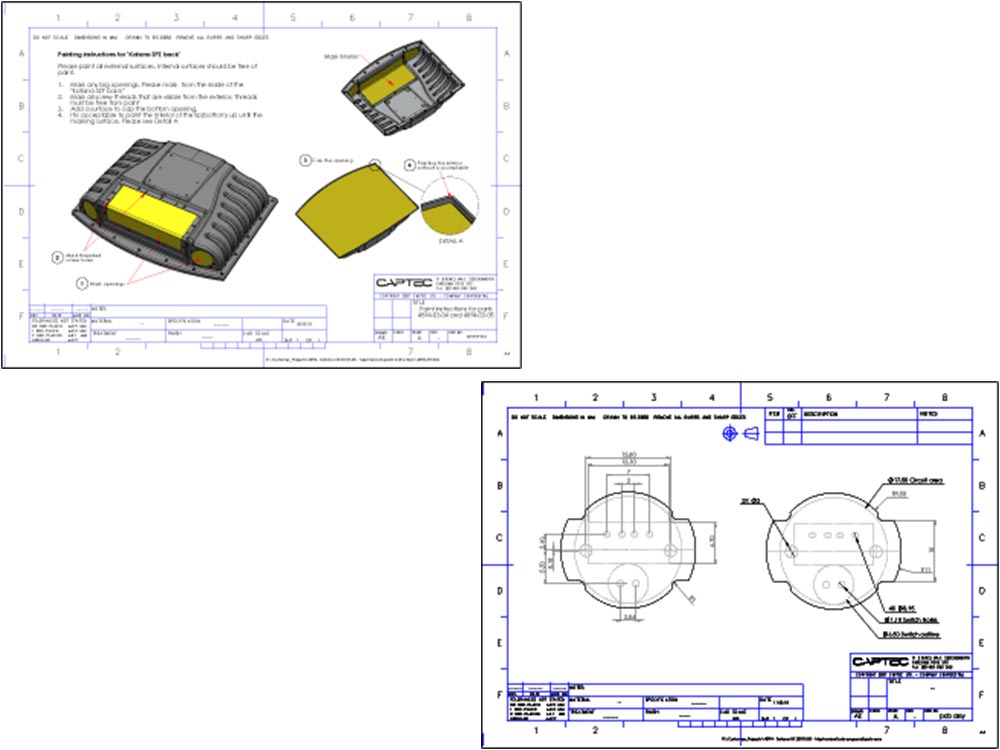
Manufacturing drawings
Throughout the project i med a series of drawings detailing parts for production. Above, masking instructions for paint shop and PCB outlines..
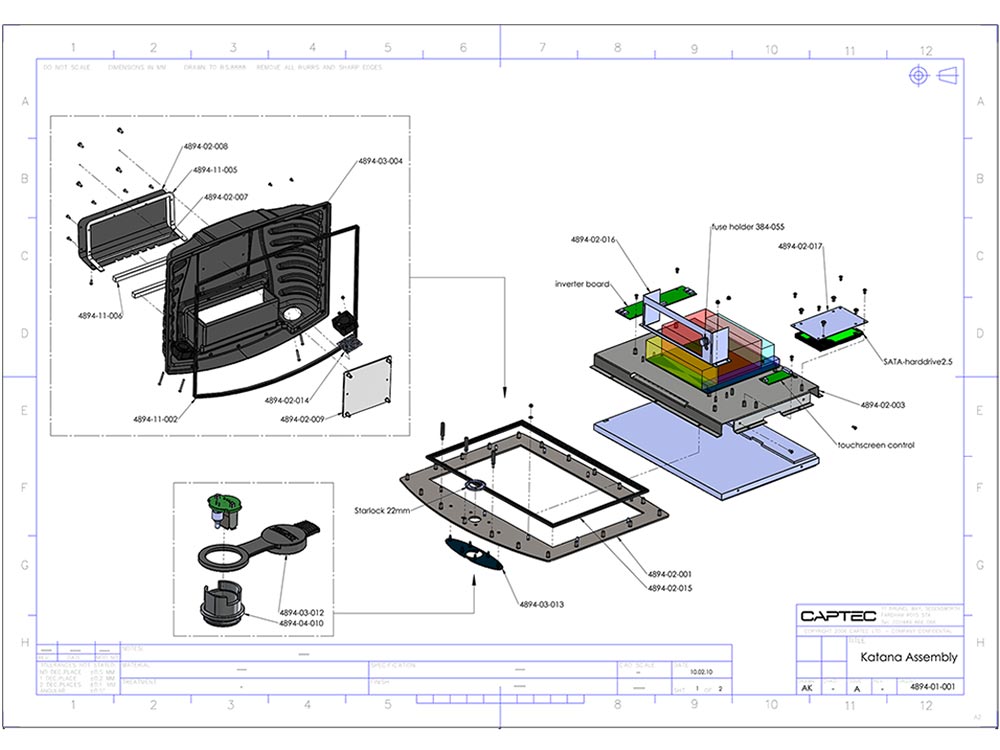
Designed for assembly
The design aim to make assembly as easy as possible. The front bezel has CNC welded studs and other features to mount parts. The majority of the assembly is literally stacking parts and thus reducing time and labor cost.